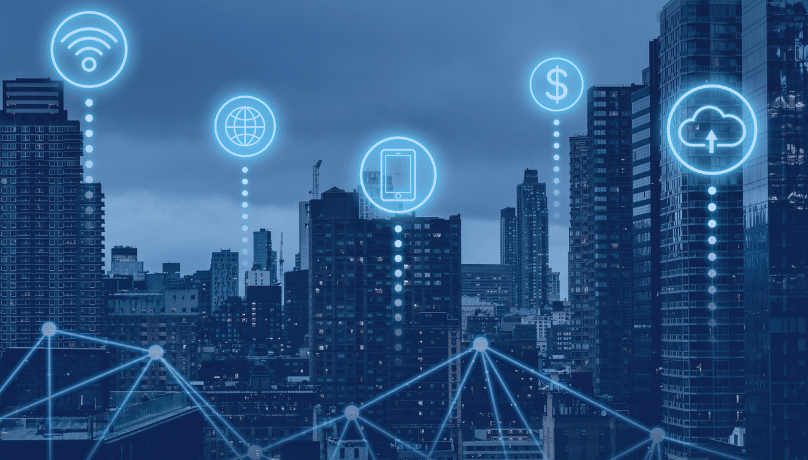

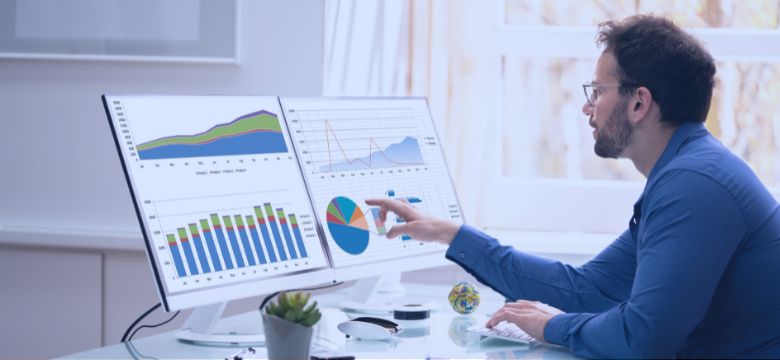
In today’s rapidly evolving business landscape, digital transformation has become a critical imperative for manufacturers seeking to remain competitive and drive growth. The manufacturing industry is undergoing a profound shift, with innovative technologies reshaping traditional processes and opening up new opportunities for efficiency, agility, and data-driven decision-making. As manufacturers embrace digital transformation, they are unlocking a wealth of use cases that can streamline operations, enhance product quality, and ultimately, deliver superior customer experiences.
The adoption of digital technologies in manufacturing offers a multitude of benefits. By leveraging advanced tools and data-driven insights, manufacturers can achieve increased productivity, improved quality control, reduced operational costs, and enhanced agility in responding to market demands. Moreover, digital transformation fosters a culture of data-driven decision-making, empowering organizations to make informed choices based on real-time information and predictive analytics.
Learn more about Digital Transformation: What is Digital Transformation?
The Industrial Internet of Things (IIoT) is revolutionizing the way manufacturers monitor and optimize their operations. By deploying a network of connected sensors and devices, companies can collect real-time data from machines, assembly lines, and production environments. This data can be analyzed to monitor performance, predict maintenance needs, and identify opportunities for process optimization. For example, sensor-enabled predictive maintenance solutions can detect potential equipment failures before they occur, minimizing downtime and maximizing asset utilization.
Have a look at IoT technology: What is the IoT and its applications
The manufacturing industry generates vast amounts of data from various sources, including production lines, supply chains, and customer interactions. By leveraging big data analytics, manufacturers can gain valuable insights into production bottlenecks, resource allocation, and product quality. For instance, analyzing machine performance data can help identify inefficiencies and enable targeted improvements, ultimately leading to increased productivity and cost savings.
Artificial Intelligence (AI) and Machine Learning (ML) are playing an increasingly significant role in manufacturing, enabling advanced automation, process control, and predictive maintenance. AI-powered quality control systems can analyze product images or sensor data to detect defects with high accuracy, ensuring consistent quality standards. Additionally, ML algorithms can be trained to optimize machine parameters, reducing waste and improving overall equipment effectiveness (OEE).
About AI technology: What is AI? Everything to know about Artificial Intelligence (AI)
Cloud computing is transforming the manufacturing industry by providing scalable, flexible, and cost-effective solutions for data storage, remote access, and application deployment. Cloud-based manufacturing enables real-time collaboration, seamless integration of supply chain partners, and access to production data and applications from anywhere, fostering agility and responsiveness to market demands.
Digital twins are virtual replicas of physical assets, processes, or entire production lines. These digital representations enable manufacturers to simulate, test, and optimize production processes before implementation, reducing risk and minimizing downtime. By leveraging digital twins, manufacturers can identify potential issues, experiment with different scenarios, and refine processes before applying changes to the physical environment.
Additive manufacturing, or 3D printing, is revolutionizing the way products are designed, prototyped, and produced. This technology enables on-demand manufacturing, rapid prototyping, and the creation of complex structures that would be difficult or impossible to produce using traditional methods. By leveraging 3D printing, manufacturers can reduce lead times, minimize waste, and explore innovative product designs.
Augmented Reality (AR) and Virtual Reality (VR) are transforming the way manufacturers approach training, maintenance, and design visualization. AR can overlay digital information and instructions onto real-world environments, enabling remote assistance for maintenance tasks or providing step-by-step guidance for complex assembly processes. VR, on the other hand, can create immersive training simulations, allowing operators to practice procedures in a safe, virtual environment before applying their skills on the production floor.
The digital transformation use cases of the manufacturing industry are well underway, and the opportunities for innovation and growth are vast. By embracing technologies such as the Industrial Internet of Things (IIoT), big data analytics, artificial intelligence, cloud computing, digital twins, additive manufacturing, and augmented/virtual reality, manufacturers can unlock new levels of efficiency, quality, and agility. At ITC Group, we understand the challenges and complexities involved in implementing digital transformation initiatives within the manufacturing sector. Contact us today to learn more about our digital transformation consulting services for manufacturing and discover how we can help you stay ahead of the curve in an increasingly competitive market.
Stay ahead in a rapidly changing world with our monthly look at the critical challenges confronting businesses on a global scale, sent straight to your inbox.